Production
The heart of the company beats thanks to its long-standing experience and the continuous introduction of new technologies.
Thermographic studies, lubricating technologies, an internal die emergency repair and maintenance department, contribute to the definition of the correct production parameters, to make each process stable and reliable.
The raw materials are always procured from market leaders to guarantee utmost reliability and traceability, as well as the correct chemical parameters that are controlled for each delivery.
The preparation of the alloy baths is entrusted to a dedicated department with 3 smelting furnaces and a degassing plant to supply the 14 production units.
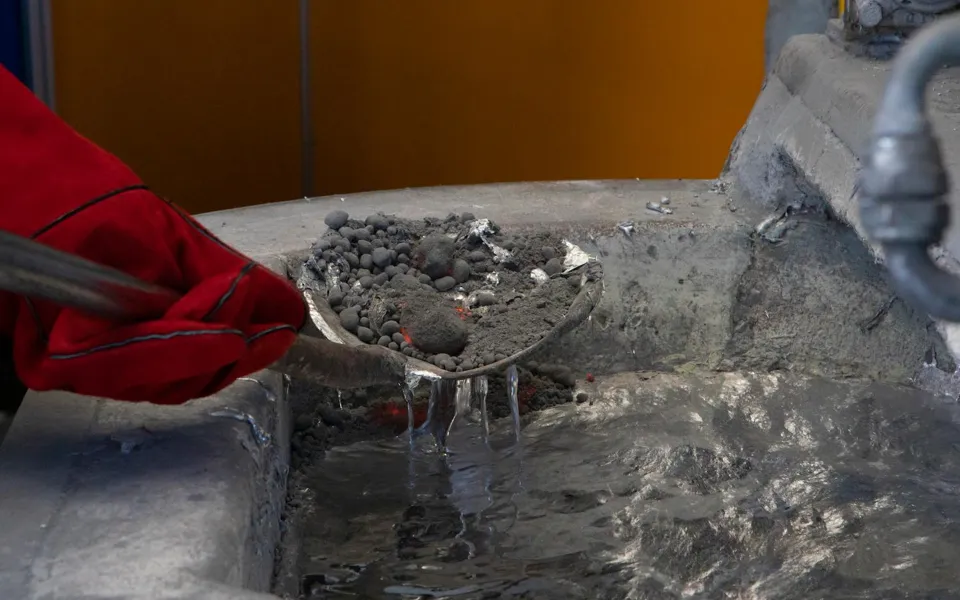
Production
The heart of the company beats thanks to its long-standing experience and the continuous introduction of new technologies.
Thermographic studies, lubricating technologies, an internal die emergency repair and maintenance department, contribute to the definition of the correct production parameters, to make each process stable and reliable.
The raw materials are always procured from market leaders to guarantee utmost reliability and traceability, as well as the correct chemical parameters that are controlled for each delivery.
The preparation of the alloy baths is entrusted to a dedicated department with 3 smelting furnaces and a degassing plant to supply the 14 production units.
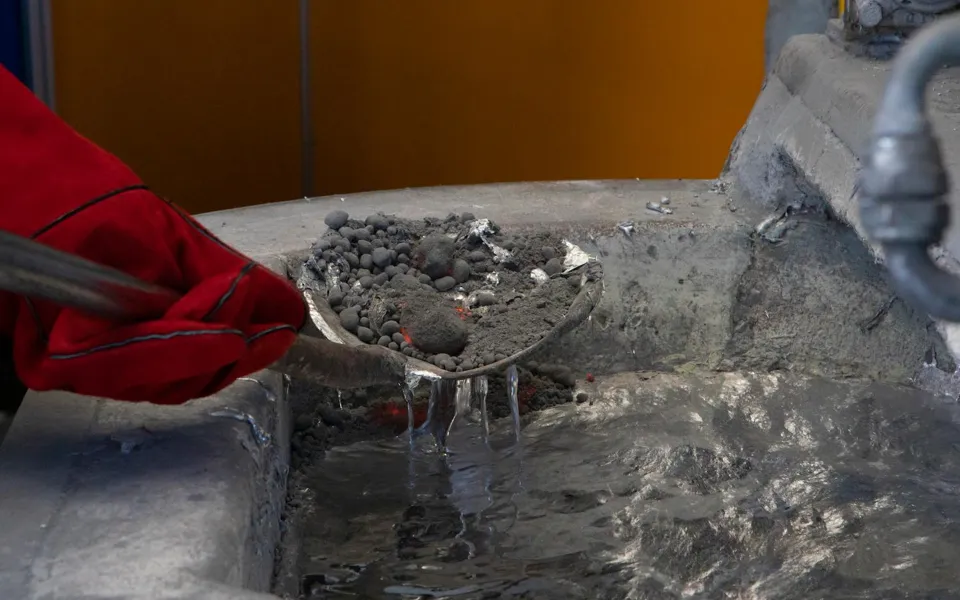
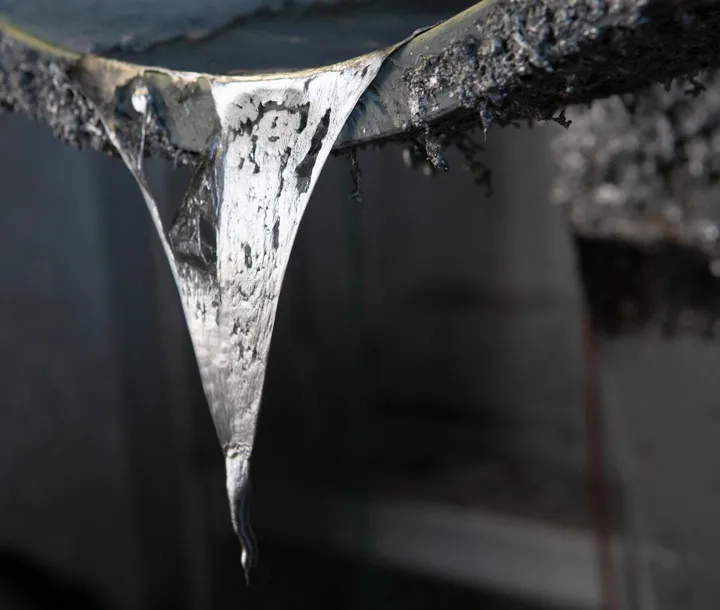
DIE CASTING UNITS
Each die casting unit has a press (with tonnage of between 420 tons and 1400 tons), a holding furnace, electronic control of heat regulation, an anthropomorphic arm to unload the dies and loading of the inserts into the die, infra-red control of the cast part, air cooling and burr trimmer.
We also have 5 mobile Vacuum Systems to use for products that require this technology.
The Burr chamber is fully automated to guarantee uniformity and repeatability of undercuts and burrs, as well as an excellent and constant result over time.
Each plant is connected to the company’s IT system to have as large a database as possible. It is also possible to control the unit remotely, thanks to an advanced industrial automation system.
TOWARDS AUTOMATION
In 2020 we fitted one of the 1400 ton plants with a fully automatic deburring chamber. In 2021 this solution was replicated with a second offline deburring chamber.
Day after day, FAR srl’s investments are aimed at automation, to guarantee maximum precision and stability of the process.
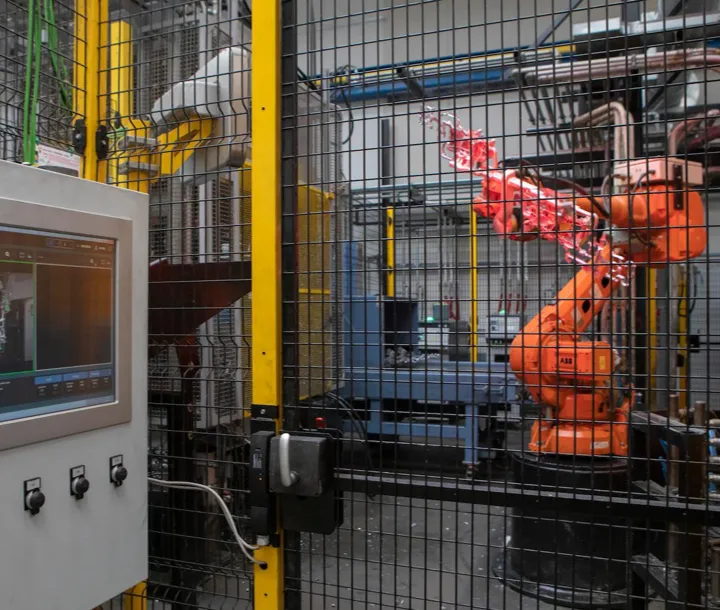
Production
-
14 autonomous production units
-
Press
-
Complete control of the plant’s parameters
-
Centralised smelting furnaces and local holding furnaces with remote level indicator
-
On-line burr trimmer
-
Anthropomorphic robot/6 axles
-
Cooling of dies
-
Electronic control of heat regulation
-
Connection to the IT system
-
Vacuum System
-
Burr chamber/automated trimming
Presses
-
Single-brand Colosio machinery
-
Presses with capacity of between 420 and 1400 tons
-
Automated presses connected to the company’s data management system
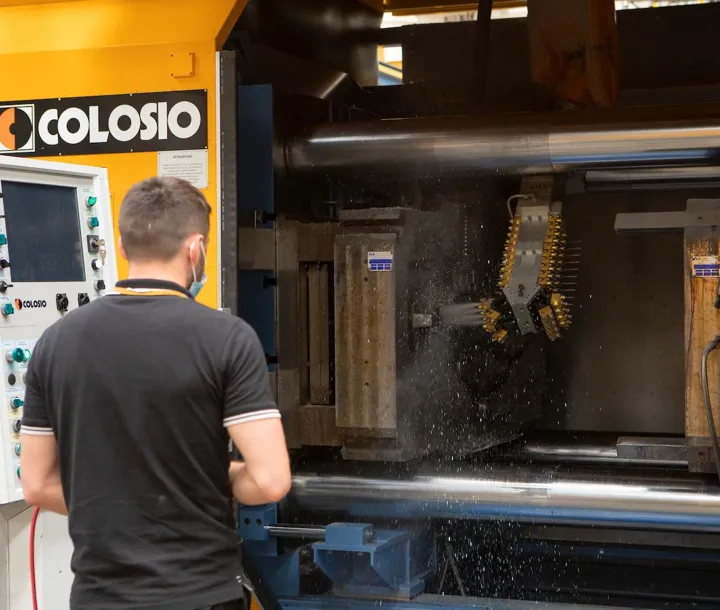
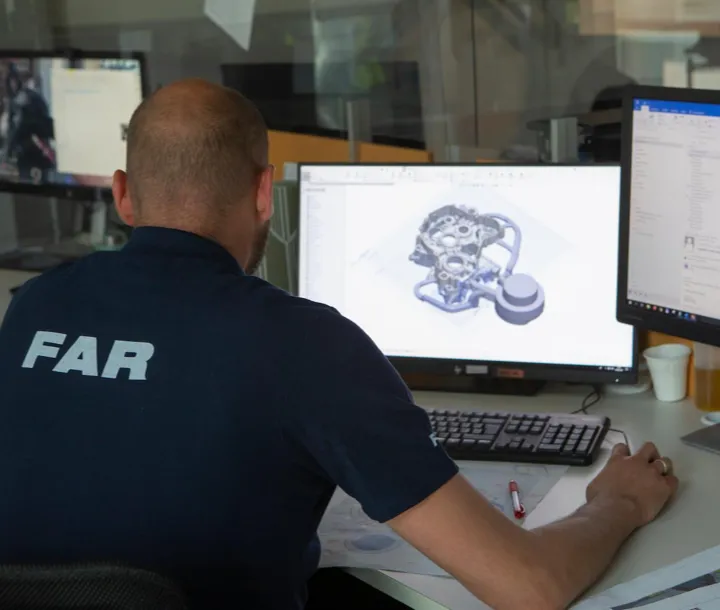
TECHNICAL OFFICE
CAD 3D-Solidworks (Dessault Systèmes) design software and FEM-Pro Cast (ESI group) casting simulation software are used for the development and optimisation of the die casting system and of the item to manufacture.
-
Design software – Solidworks
-
Simulation software – Pro Cast
QUALITY OFFICE
The quality laboratory has a metallurgical testing area and a measuring and inspection area, both set up and improved over time to meet all the client’s needs.
The department is equipped with: A Zeiss 3D coordinate-measuring machine (CMM) for dimensional controls; a Spectrometer for analysis of the casting alloy; a Digital microscope for metallographic analysis; an X-ray machine with integrated tomography for in-depth control and initial type-testing of the products.
- Dimensional controls
- Coordinate-measuring machine (CMM)
- Digital microscope
- Roughness tester
- Alloy analysis – Spectrometer
- X-ray machine
- Quantometer
- Electronic thickness gauge
- Leak test benches
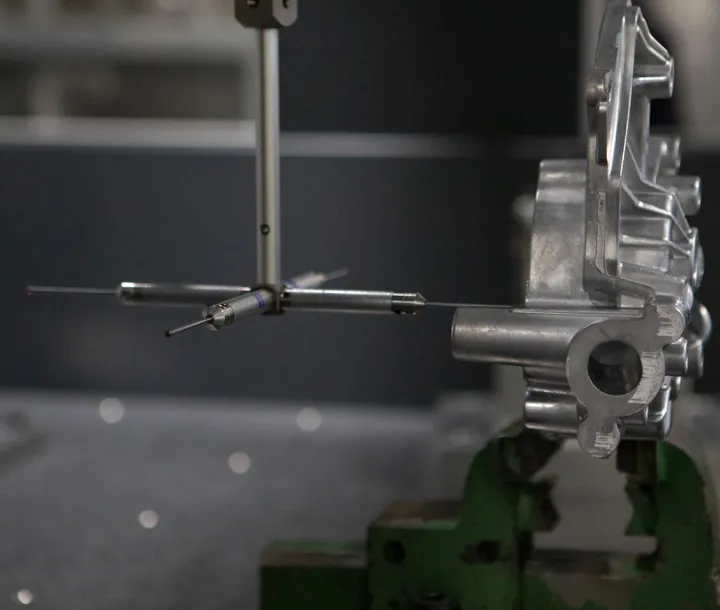
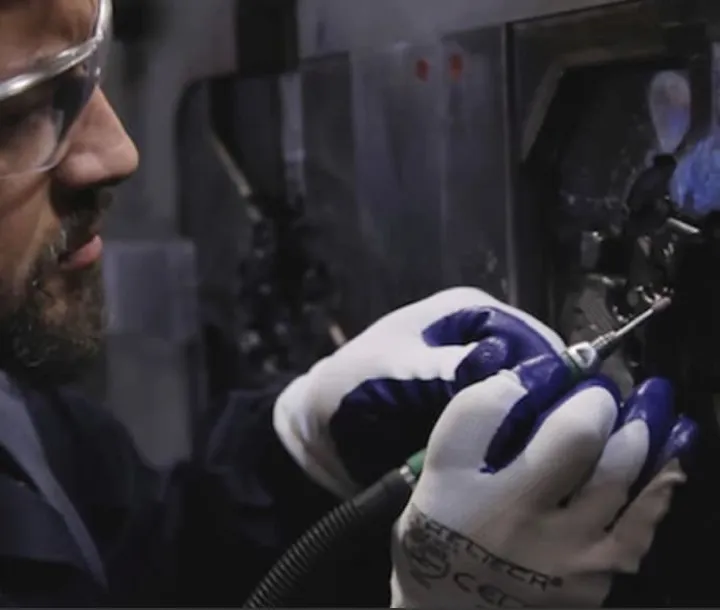
DIE MAINTENANCE
Die maintenance is performed in the new internal department equipped with CAD-CAM and CNC machining centres.
Die maintenance activities are managed and programmed by the company’s IT system.
At the end of each lot production cycle, the Technical, Quality and Production Departments report the adjustments to be made to the equipment for future cycles. Only after the Maintenance Department has completed its activities will the die once again be “Productive” and be available for the next lot.
- CAM simulation
- CNC machining